Basic Info.
Model NO.
XK-Cr
Application
Decorative Coating
Free Sample
Available
Packing
Vacuum Packed
Certificate
Coa, Coc
Delivery
10-20 Days
Transport
by Air, by Sea
Certificate of Origin
Available
Transport Package
Vacuum Sealed
Specification
100mm dia. x 45mm, 95mm dia. x 45mm, 63 x 32mm
Trademark
no
Origin
China
HS Code
848690
Production Capacity
2000PCS/Month
Product Description
Features of chromium arc targets
Chemical Composition: pure Cr
Available Purity: 2N5, 2N8, 3N, 3N5
Production Technology: HIP
Shapes: planar targets, rotary targets
Average Grain Size: < 100um
Application of chromium arc targets
Chromium arc target are produced by HIP technology, usually used for decorative coating to obtain metal color film. With up to 3N5 purity, uniform grain size, lower impurity content, end user can obtain good hardness, high brightness, corrosion and oxidation resistant color without fading for a long time. We have been supplying chromium sputtering targets, chromium arc cathodes for manufacturers of watch, sanitary ware, car mirrors, etc, which are suitable for various magnetron sputtering machines and ionic plating machines.
Available arc targets for decorative coating:
Application of arc targets
PVD coatings have been established as the high quality surface finish for watches, sanitary and door hardware with many manufacturers marketing coated products with long time guarantees on their appearance.it offers a longer lifetime, metallic colors, scratch protection and is environmentally friendly.
Comparing to traditional electroplated coatings, PVD coating has superior hardness and wear resistance, do not discolour or tarnish, have reasonably high corrosion resistance and do not suffer under UV radiation and so for example PVD Coating wheels and PVD coated watches, in particular DLC coated black PVD watches have proved popular.
PVD coatings can be deposited with a wide colour range. Metals used as target material in decorative PVD processes are zirconium, titanium, chromium, titanium-aluminum alloys and niobium. Ceramic coatings are deposited to increase the hardness of the coating. This is achieved by introducing reactive gases during the deposition process. The most widely used reactive gases for decorative coatings are nitrogen and methane or acetylene to produce metal-nitride, metal-carbide, metal-carbonitride and diamond like carbon DLC coatings. Also oxygen can be used to produce oxides, oxinitrides, etc. The decorative coatings are produced in a certain colour range, depending on the metal-to-gas ratio in the coating and the structure of the coating. Both of these factors can be altered by changing the deposition parameters.
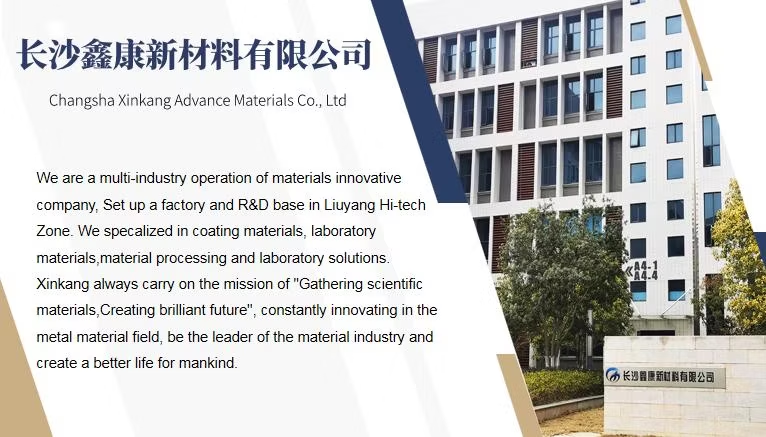





Chemical Composition: pure Cr
Available Purity: 2N5, 2N8, 3N, 3N5
Production Technology: HIP
Shapes: planar targets, rotary targets
Average Grain Size: < 100um

Application of chromium arc targets
Chromium arc target are produced by HIP technology, usually used for decorative coating to obtain metal color film. With up to 3N5 purity, uniform grain size, lower impurity content, end user can obtain good hardness, high brightness, corrosion and oxidation resistant color without fading for a long time. We have been supplying chromium sputtering targets, chromium arc cathodes for manufacturers of watch, sanitary ware, car mirrors, etc, which are suitable for various magnetron sputtering machines and ionic plating machines.
Available arc targets for decorative coating:
Target / cathode Materials | Purity | Color of coating films |
Ti | 2N5, 2N7 | Golden yellow, light yellow, golden |
Cu | 3N5 | |
Zr | 2N4 | |
Ag | 4N | Silver |
Cr | 2N5, 2N8, 3N, 3N5 | |
Al | 2N5, 3N, 4N | |
Sn | 3N, 4N | |
TiAl | 2N6 | Black, gun black, steel |
Si | 5N | |
SUS 304, 316, 316L | 2N | |
SiO2 | 4N | Steel color, tungsten steel color |
TiO2 | 3N5 | Transparent color, rainbow color |
SiAl | 3N |
Application of arc targets
PVD coatings have been established as the high quality surface finish for watches, sanitary and door hardware with many manufacturers marketing coated products with long time guarantees on their appearance.it offers a longer lifetime, metallic colors, scratch protection and is environmentally friendly.
Comparing to traditional electroplated coatings, PVD coating has superior hardness and wear resistance, do not discolour or tarnish, have reasonably high corrosion resistance and do not suffer under UV radiation and so for example PVD Coating wheels and PVD coated watches, in particular DLC coated black PVD watches have proved popular.
PVD coatings can be deposited with a wide colour range. Metals used as target material in decorative PVD processes are zirconium, titanium, chromium, titanium-aluminum alloys and niobium. Ceramic coatings are deposited to increase the hardness of the coating. This is achieved by introducing reactive gases during the deposition process. The most widely used reactive gases for decorative coatings are nitrogen and methane or acetylene to produce metal-nitride, metal-carbide, metal-carbonitride and diamond like carbon DLC coatings. Also oxygen can be used to produce oxides, oxinitrides, etc. The decorative coatings are produced in a certain colour range, depending on the metal-to-gas ratio in the coating and the structure of the coating. Both of these factors can be altered by changing the deposition parameters.


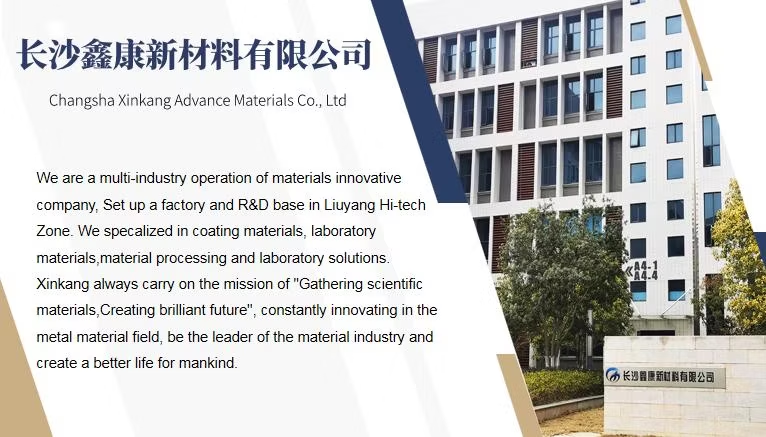





